The same team of highly experienced technicians operate all the dynamics capabilities, backed by specialist scientific and engineering expertise.
The team supports customers to understand the dynamic behaviour of satellites in response to a wide range of stimuli to replicate its complete journey to orbit. Digital models that predict behaviour can be validated with physical testing under a range of conditions enabling complete characterisation of its dynamic behaviour.
Learn more about which of our facilities is right for you:
Vibration facility
- Shaker thrust 67kN
- Shaker load capacity 1 tonne
- Crane capacity is 1 tonne
- Crane hook height is 5.388m
- Access doors – size 3.5m wide x 3.5m high
- 3 axis sine, random and shock capabilities
- 64 channels of monitoring
- 67 kN thrust
- 64 mm stroke
- Clean room standard not specific, but expected to be class 8 (100,000) – test items normally bagged
Pyro-shock facility
The pyro-shock tests simulate separation of the satellite from the launch vehicle adapter.
- Pyro-shock rig for sub-system tests (<50 kg)
- Full-scale separation and deployment tests
- Clamp band release tests
Acoustic
The acoustic test facility will simulate the acoustic environment under the fairing of the launch vehicle during launch. The acoustic noise levels inside the facility will typically reach 146 dBA with a frequency content ranging from 30 Hz to 10,000 Hz.
Acoustic testing
- ISO8 clean room conditions (with temperature and humidity control)
- Direct field acoustic noise testing approach
- Flexible and modular arrangement simulates a wide variety of test conditions appropriate to the specific test article
- Driven by high power amplifiers (>0.5 MW)
- Sound pressure level 146 dB
Mass properties
Measurement of the mass properties of satellites is an important test needed to confirm its mass and coordinates of its centre of mass. Sometimes it is also required to measure the moments of inertia and products of inertia. This facility is used to measure a satellite's mass properties to ensure that it is consistent with its design parameters. The facility will use a Resonic 6000F machine, a novel resonant mass system which measures properties by very low level and low displacement vibration.
Physical properties facility
- ISO8 clean room conditions (with temperature and humidity control)
- Centre of mass
- Moments of inertia
- Products of inertia
Vibration and shock 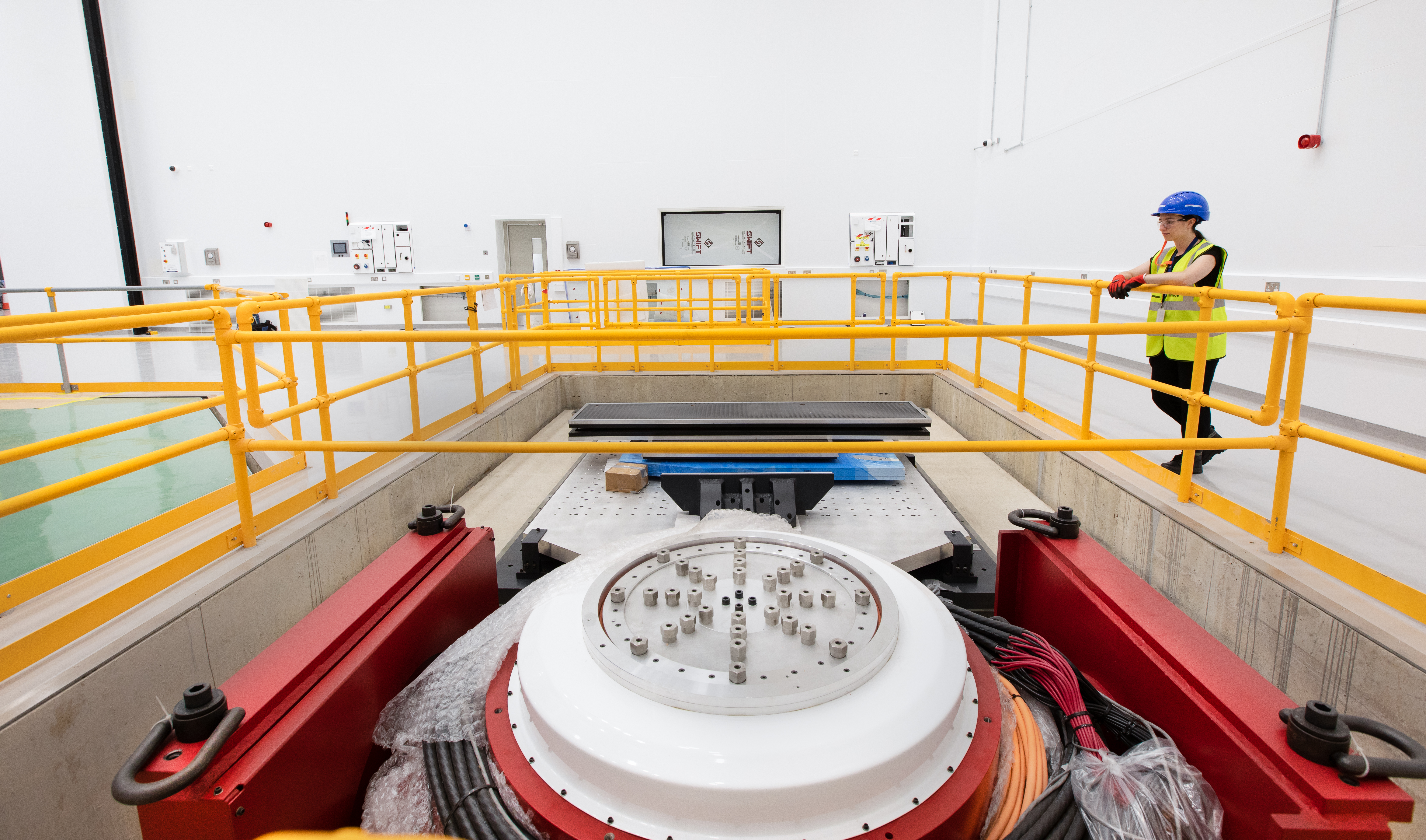
The vibration test facility will vibrate satellites in three axes over a frequency range of 5 to 150 Hz and acceleration levels from 1.5g. The facility will also be able to subject large sub-assemblies to random vibration environments up to 2000Hz.
Vibration testing
- ISO8 clean room conditions (with temperature and humidity control)
- Separate vertical and horizontal vibration facilities, both with large guided interface areas to accommodate large and heavy test articles
- 222 kN sine force, 76 mm stroke 5 to 2,000 Hz frequency range
- Solid state power amplifier with soft shutdown
- 64 control channels
Shock and deployment testing
- Full-scale separation and deployment tests
- Clamp band release tests
Data analysis support
- 512 channel data acquisition system supporting the complete dynamics test suite
- A large stock of accelerometers for rental to test customers
- Data capture also available through high-speed camera and force measuring devices
- Modelling and digital twin capability in development
How to access our facilities
As the UK's national space laboratory, we occupy a unique and independent position between industry, academia and government. Our facilities are open to everyone on a commercial basis, whether based in the UK or internationally.
To enquire about use of our test facilities please:
For further information, please read the NSTF frequently asked question page.
Images:
Image 1 - Vibration table in RAL Space. Credit: STFC RAL Space
Image 2 - Vibration suite in NSTF. Credit: STFC RAL Space