We provide a range of services from conceptual studies and detailed analysis, through to the definition and management of thermal tests. We also design, manufacture and procure thermal hardware such as multilayer insulation blankets. We have particular expertise in cryogenic engineering, planetary and lunar missions, ground-based telescopes and electronics thermal control. We operate to an
ISO 9001:2015 certified Quality Management System.
Conceptual Studies
At the conceptual design stage fundamental trade-offs are made. Firstly all heat sources are identified. Internal heat can be generated by items such as electronic equipment and batteries, whereas external heat is largely due to solar radiation and planet infra-red flux.
Once all heat sources have been identified it is necessary to find means to reject heat or to keep certain components warm. Various architectures are assessed and, broadly speaking, a decision is made on whether to use a passive or an active architecture.
Passive hardware dissipates no electrical power and has no mechanically activated moving parts. For example, radiators, surface coatings, heat pipes and multilayer insulation (MLI).
RAL Space specialises in the design and manufacture of MLI for instruments and small spacecraft.
Active hardware may employ power or moving parts. For example, heaters, louvres, coolers and thermal switches.
In general it is desirable to use a passive architecture wherever possible to minimise cost, mass, power and risk. However, most instruments will require heaters and many will also have thermal requirements which can only be met by the use of advanced active methods. Initial trade-off studies which weigh up the advantages and disadvantages of a range of passive and active options are important in the optimisation of the thermal control subsystem.
Preliminary studies are performed using Microsoft® Excel or specialised thermal modelling software packages such as ESATAN-TMS.
Detailed Design
The thermal mathematical analysis of spacecraft and instruments generally employs the finite difference method for temperature and heat flux predictions and the software used at RAL for this task is the industry standard European Space Agency (ESA) software, ESATAN-TMS.
Geometrical models
To calculate the radiative heat transfer matrix, a necessary prerequisite for the thermal model, a geometrical mathematical model (GMM) must be established which is representative of the structural configuration and the surface properties used.
Environmental loads
The GMM is also used to calculate the environmental loads from the Sun and Planet which depend on the orbit and attitude of the spacecraft.
Design cases
A number of design cases representative of extreme operational and non-operational conditions are mathematically simulated to ensure that the instrument remains in a safe thermal condition throughout the mission life.
Systems engineering approach
The systems engineering approach is enhanced by interaction with RAL Space's engineers and scientists in other relevant disciplines including mechanical design, optical design, stray light, contamination control, electrical and electronics engineering, systems engineering and applied physics.
Testing and correlation
A thermal balance test, in which a hardware model is put in a vacuum chamber and the thermal conditions of space are simulated, is usually performed to verify the thermal control subsystem and to provide data against which the mathematical model can be improved or correlated.
Our thermal engineers are experienced at writing test specifications and procedures and correlating test results with our thermal models. RAL Space's Assembly Integration and Verification Group on site can provide environmental testing facilities and clean assembly rooms.
Ground-based telescopes
Although our main focus is spacecraft payloads, we also carry out thermal design and analysis for ground based telescopes. ALMA, FMOS and VISTA are among our recent projects.
ALMA
The UK is participating in the construction of the Atacama Large Millimetre Array (ALMA) in the Atacama Desert of Northern Chile. The ALMA Observatory will have 64 twelve-metre diameter telescopes working together as an interferometric imaging array equivalent to a single telescope 15km in diameter. We provided thermal analysis of the cryogenic detector system down to 4K.
FMOS
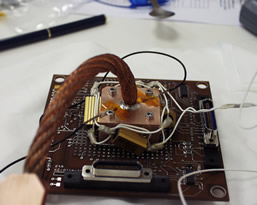
The Fibre-Multi-Object Spectrograph (FMOS) is a collaboration to design and construct a fibre-fed infrared spectrograph system for the Subaru 8m telescope on Mauna Kea in Hawaii. RAL Space has overall responsibility for the thermal and optical design of the spectrograph. We have designed a system to cool the detector to 70K using a Sumitomo CH-210 Gifford-McMahon cryocooler.
VISTA Camera
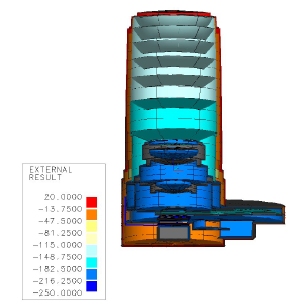
The Visible and Infrared Survey Telescope (
VISTA) for Astronomy is a 4m diameter wide-field survey telescope dedicated to conducting detailed imaging surveys of the sky. The telescope began operations at the Cerro Paranal Observatory in Chile during 2007.
RAL Space were responsible for the thermal engineering of the three tonne infra-red camera. The design utilises three two-stage Leybold 5/100T cryocoolers. The first stage cools the optical bench and optics to around 100°K, whilst the second stage cools the detectors to < 77°K.
The success of the design hinges on the optimisation of heat flow to minimise thermal loads on the detectors whilst holding external temperatures very close to ambient to reduce misting and convective disturbances in the field of view.
For more information please contact:
RAL Space Enquiries